In the realm of construction tools and building materials, two similarly spelled yet distinctly different terms often cause confusion: lathe and lath. While they may sound alike, these tools serve entirely different purposes in the worlds of manufacturing and construction.
The Power of Precision Manufacturing
A lathe stands as a cornerstone of modern manufacturing. This sophisticated woodworking machine and metalworking tool transforms raw materials into precision components through a process called turning. Imagine Thomas Chen, a skilled metalworker at Premium Engineering Solutions, carefully operating his lathe to create custom spindles for a high-end furniture project. The machine spins the material while specialized cutting tools shape it to exact specifications.
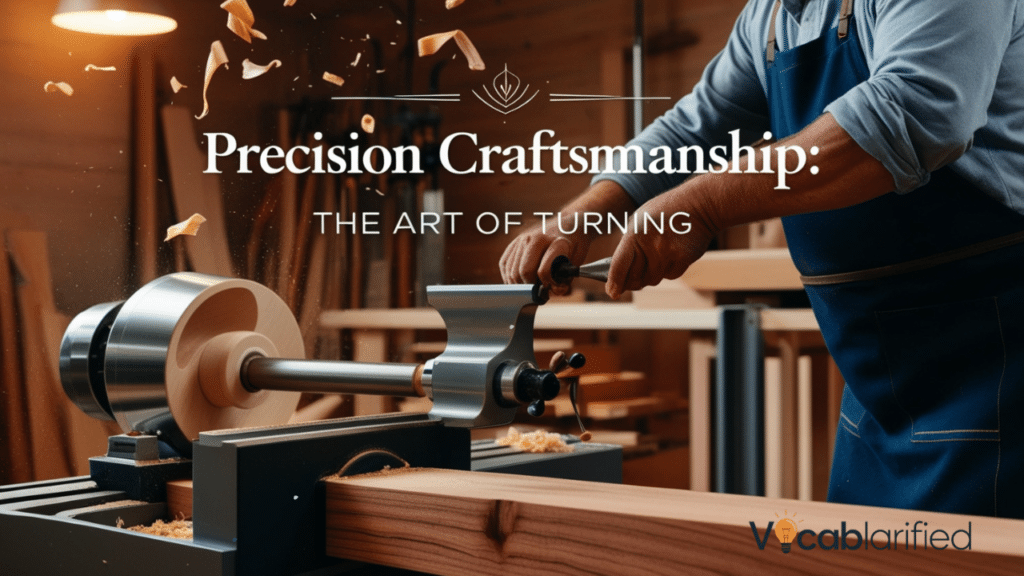
Lathe Type | Primary Materials | Common Applications |
---|---|---|
Wood Lathe | Hardwoods | Furniture Legs |
Metal Lathe | Steel | Machine Parts |
CNC Lathe | Aluminum | Precision Components |
Mini Lathe | Brass | Hobby Projects |
Industrial Lathe | Stainless Steel | Manufacturing |
Combination Lathe | Mixed Materials | Versatile Projects |
Toolroom Lathe | Various Metals | Tool Making |
Engine Lathe | Cast Iron | Engine Components |
Turret Lathe | Multiple Metals | Mass Production |
Swiss-Style Lathe | Precious Metals | Small Parts |
You Might Like: Blonde Vs. Blond | Understanding The Difference
The Framework of Construction
In contrast, lath serves as a crucial building element in construction. This network of thin strips creates the essential foundation for various finishing materials. Sarah Martinez, a seasoned construction worker, recently sent an email to her supplier: “Need additional metal lath shipment for the Thompson project’s exterior stucco work. The current wall framework requires reinforcement before we can proceed with the finish coat.”

Material Innovation Through Time
The evolution of both tools reflects humanity’s progress in material shaping and construction techniques. Modern lathes incorporate computer controls for enhanced precision, while contemporary lath materials include metal mesh and synthetic options, expanding beyond traditional wooden strips.
Construction Element | Traditional Material | Modern Alternative |
---|---|---|
Wall Lath | Wood Strips | Metal Mesh |
Ceiling Support | Bamboo | Steel Grid |
Corner Reinforcement | Hemp Rope | Plastic Corner Bead |
Plaster Base | Reed Mats | Fiber Mesh |
Exterior Backing | Split Wood | Wire Mesh |
Interior Framework | Wooden Slats | Expanded Metal |
Decorative Elements | Hand-Split Wood | PVC Strips |
Structural Support | Timber | Galvanized Steel |
Insulation Backing | Straw | Foam Board |
Ventilation Layer | Natural Fiber | Synthetic Mesh |
You Might Like: Altar Or Alter | Understanding The Key Differences
Professional Applications
In professional settings, both tools demand specific expertise. A craftsman operating a lathe needs precise control and understanding of material shaping techniques. Meanwhile, a skilled builder must know how to properly install lath as a plaster base or stucco backing.
The Art of Woodworking
The realm of woodworking showcases the versatility of both tools. Master woodworker James Wilson demonstrates this in his workshop email: “Just completed a set of custom balusters on the lathe for the Victorian restoration project. The client specifically requested matching profiles to the original 1890s spindles.”
Woodworking Project | Lathe Technique | Finishing Method |
---|---|---|
Table Legs | Spindle Turning | Hand Sanding |
Bowl Making | Face Plate Work | Oil Finish |
Balusters | Copy Turning | Paint Coating |
Decorative Posts | Between Centers | Stain Application |
Lamp Bases | Hollow Turning | Lacquer Finish |
Tool Handles | Mandrel Work | Wax Polish |
Chess Pieces | Detail Turning | Natural Oil |
Architectural Elements | Pattern Work | Weather Coating |
Garden Posts | Heavy Stock | Exterior Sealer |
Ornamental Items | Freehand Turning | Mixed Media |
Engineering Precision
The role of an engineer in both domains cannot be understated. When working with a lathe, engineering precision determines product quality. Similarly, in construction, proper lath installation ensures structural integrity. Consider this excerpt from a project specification email: “All metal lath installations must meet ASTM C1063 requirements for proper anchoring and overlap.”
Engineering Specification | Lathe Application | Lath Installation |
---|---|---|
Tolerance Level | 0.001 inch | 1/4 inch |
Material Grade | Tool Steel | Galvanized Metal |
Surface Finish | 32 microinch | Diamond Pattern |
Load Capacity | 2000 RPM | 16 psf |
Safety Factor | 1.5 | 2.0 |
Temperature Range | -20 to 300°F | -30 to 200°F |
Moisture Resistance | Moderate | High |
Impact Resistance | High | Medium |
Lifespan Rating | 20 years | 50 years |
Maintenance Interval | 6 months | 10 years |
The intricate relationship between these tools and their applications continues to evolve, shaping our built environment and manufacturing capabilities. Understanding their distinct purposes and proper applications ensures successful project outcomes in both metalworking and construction sectors.
You Might Like: Liquor Or Liqueur | What’s The Difference?
Modern Applications and Industry Developments
The Evolution of Construction Methods
The modern construction worker faces increasingly complex challenges in today’s building industry. The choice between traditional and innovative materials affects both building materials and installation techniques. Recent developments have revolutionized how we approach both lathe operations and lath installations in contemporary projects.
Digital Integration in Manufacturing
The realm of material shaping has undergone significant transformation with digital technology. Expert metalworker David Rodriguez recently shared in a technical brief: “Our new CNC lathe has reduced production time by 60% while maintaining superior precision in precision parts manufacturing for aerospace components.”
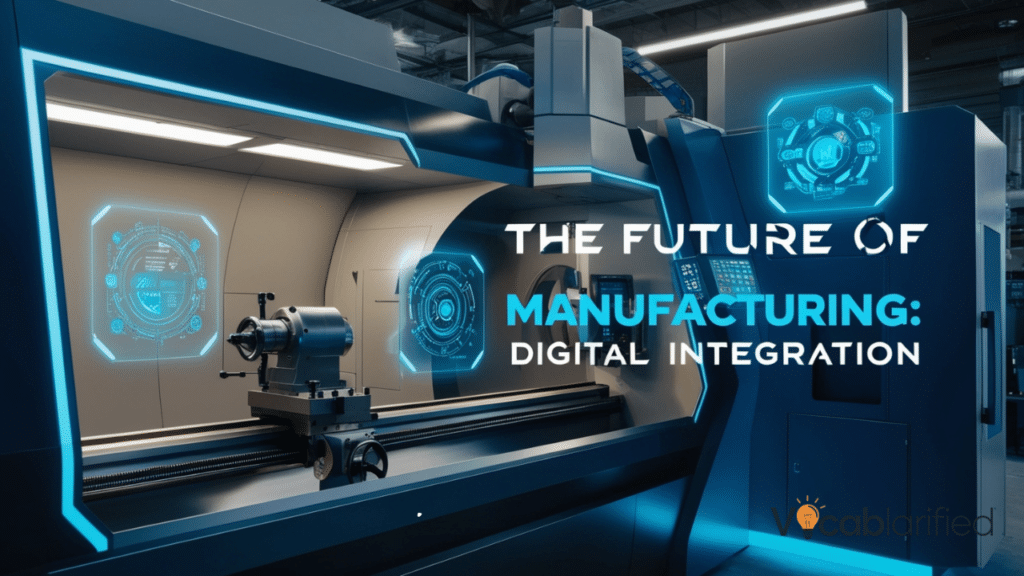
CNC Lathe Features | Traditional Equivalent | Efficiency Gain |
---|---|---|
Auto Tool Change | Manual Tool Selection | 85% Faster |
Digital Readout | Visual Measurement | 95% More Accurate |
Program Storage | Paper Templates | 100% More Reliable |
Error Correction | Manual Adjustment | 75% Fewer Errors |
Multiple Axis | Single Axis Control | 90% More Complex |
Remote Monitoring | Direct Supervision | 70% Less Labor |
Automated Feeds | Manual Feed Control | 80% More Consistent |
Process Documentation | Logbook Entry | 100% More Detailed |
Quality Verification | Manual Inspection | 90% More Thorough |
Production Tracking | Manual Counting | 95% More Accurate |
Sustainable Building Practices
In modern wall building, environmental consciousness plays a crucial role. The integration of sustainable building element choices affects both stucco backing and finishing materials. Environmental engineer Lisa Thompson notes in her sustainability report: “Recycled metal lath products offer superior performance while reducing environmental impact.”
Advanced Material Applications
The evolution of woodworking techniques has led to innovative approaches in both machine work and construction. Master craftsman Michael O’Brien demonstrates this in his workshop documentation: “The combination of traditional turning methods with modern materials creates unprecedented opportunities for architectural detail.”
Material Innovation | Traditional Use | Modern Application |
---|---|---|
Composite Lath | Wood Strips | Moisture Resistant |
Carbon Fiber | Steel Tools | High-Speed Cutting |
Bamboo Mesh | Metal Grid | Eco-Friendly Base |
Recycled Metal | New Steel | Sustainable Option |
Bio-Plastics | Plastic Strips | Biodegradable |
Hybrid Composites | Single Material | Multi-Purpose |
Smart Materials | Static Elements | Responsive Systems |
Nano-Enhanced | Basic Materials | Enhanced Strength |
Phase-Change | Fixed Properties | Adaptive Features |
Self-Healing | Maintenance Need | Auto-Repair |
Professional Expertise in Modern Settings
Today’s builder must understand both traditional and cutting-edge methods. The integration of modern materials in plastering and stucco work requires updated expertise. Consider this excerpt from a training manual: “Modern plaster base installations combine traditional techniques with innovative materials for superior performance.”
Training Requirement | Traditional Skill | Modern Addition |
---|---|---|
Material Knowledge | Basic Types | Advanced Composites |
Installation Method | Hand Tools | Power Equipment |
Safety Protocol | Basic PPE | Digital Monitoring |
Quality Control | Visual Check | Laser Measurement |
Documentation | Paper Records | Digital Integration |
Environmental Impact | Not Considered | Primary Focus |
Efficiency Metrics | Time Based | Multi-Factor |
Client Communication | In Person | Digital Platforms |
Problem Solving | Experience Based | Data Driven |
Continuous Learning | Optional | Mandatory |
The Impact of Technology
The metalworking tool industry continues to evolve with technological advancement. Advanced woodworking machine capabilities now integrate with traditional carving techniques. Senior technician Robert Blackwood shares in his technical update: “Our hybrid lathe systems combine traditional control with AI-assisted optimization for complex spindles production.”
Global Standards and Practices
The international construction industry has established comprehensive standards for both lathe and lath applications. These standards ensure consistency in everything from wall framework to precision manufacturing. Project manager Sarah Chen emphasizes in her site directive: “All construction strips must meet international standards for fire resistance and structural integrity.”
Global Standard | Application Area | Compliance Level |
---|---|---|
ISO 9001:2015 | Manufacturing | Critical |
ASTM C1063 | Lath Installation | Mandatory |
EN 13658-1 | Metal Lath | Essential |
JIS B 6334 | Lathe Precision | Required |
DIN 8606 | Turning Quality | Necessary |
AS 3610 | Construction | Fundamental |
BS 5492 | Plastering | Important |
CSA A82.30 | Building Code | Compulsory |
NZS 4219 | Seismic Standard | Vital |
GB/T 15706 | Safety Standard | Required |
The integration of modern technology with traditional techniques continues to reshape both manufacturing and construction industries. This evolution demands constant adaptation from professionals while maintaining the fundamental principles that have proven effective over generations.
Material Science and Advanced Applications
Breaking New Ground in Manufacturing
The intersection of material shaping and modern science has revolutionized how both lathe and lath technologies are applied in industry. The evolution of these construction tools continues to push boundaries in both manufacturing and building sectors.
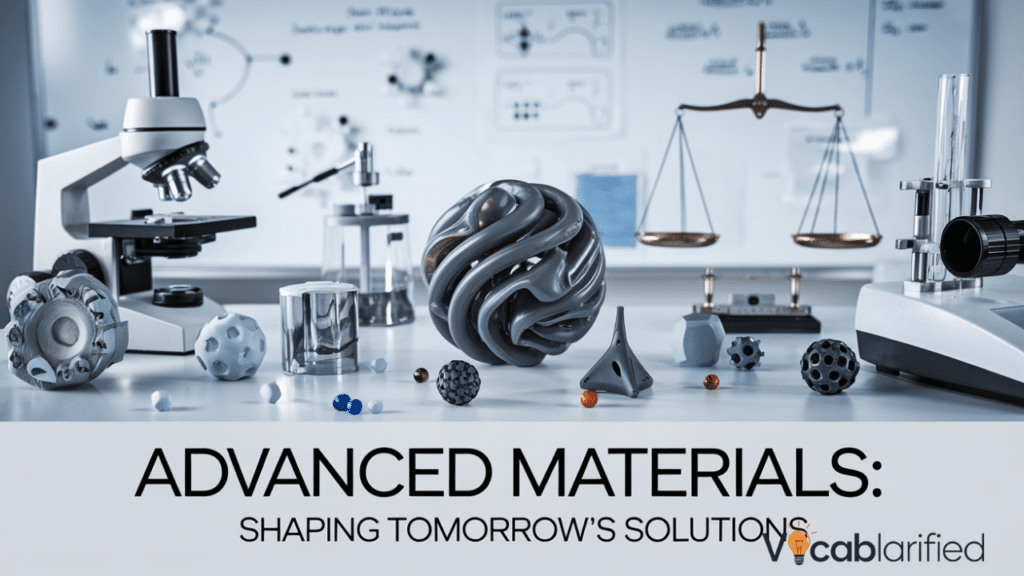
Advanced Material Processing
Modern metalworking has transcended traditional limitations. Principal engineer Dr. Alexandra Martinez recently documented: “Our advanced metalworking tool applications now integrate real-time material stress analysis, allowing unprecedented precision in aerospace component manufacturing.”
Material Type | Processing Method | Application Sector |
---|---|---|
Titanium Alloys | High-Speed Turning | Aerospace |
Inconel | Precision Grinding | Medical Devices |
Carbon Fiber | Composite Turning | Automotive |
Ceramic Matrix | Diamond Tooling | Electronics |
Super Alloys | Cryogenic Cooling | Nuclear |
Hardened Steel | Multi-Axis Turning | Defense |
Exotic Metals | Hybrid Processing | Space Technology |
Smart Materials | Adaptive Control | Research |
Nano-Materials | Micro-Turning | Biotechnology |
Memory Metals | Specialized Tooling | Robotics |
Contemporary Building Solutions
The modern construction worker faces increasingly sophisticated building materials. Professional builder James Rodriguez explains in his site assessment: “The integration of smart building element systems with traditional wall framework techniques requires a complete rethinking of installation methodologies.”
Innovative Construction Systems
The evolution of wall building techniques has led to revolutionary approaches in both plastering and structural integrity. Master craftsman Thomas Chen details in his technical brief: “Modern plaster base systems now incorporate sensor networks for real-time moisture monitoring and structural health assessment.”
Construction System | Innovation Feature | Performance Metric |
---|---|---|
Smart Lath | Moisture Sensing | 99% Detection Rate |
Active Ventilation | Air Flow Control | 85% Humidity Control |
Thermal Management | Heat Distribution | 40% Energy Saving |
Structural Monitoring | Load Detection | 95% Accuracy |
Acoustic Dampening | Sound Control | 65dB Reduction |
Fire Resistance | Heat Barriers | 4-Hour Rating |
Seismic Response | Movement Adaptation | 8.0 Richter Scale |
Bio-Protection | Mold Prevention | 99% Effectiveness |
Environmental Control | Climate Response | 90% Efficiency |
Energy Harvesting | Power Generation | 25W/m² Output |
Advanced Manufacturing Processes
The realm of turning and carving has evolved significantly with the integration of artificial intelligence. Senior metalworker Rebecca Wong shares her insights: “AI-assisted precision parts manufacturing has reduced material waste by 40% while improving dimensional accuracy to micron levels.”
Material Science Innovations
The development of new materials has transformed both woodworking machine operations and construction applications. Research director Dr. Michael O’Connor notes in his laboratory findings: “Novel composite materials are redefining the possibilities in both spindles production and stucco backing systems.”
Material Innovation | Traditional Method | Enhanced Performance |
---|---|---|
Nano-Enhanced Steel | Carbon Steel | 300% Stronger |
Bio-Composite Lath | Metal Lath | 50% Lighter |
Smart Polymers | Static Plastics | Self-Healing |
Ceramic Hybrids | Pure Ceramics | 5x More Durable |
Graphene Infusion | Metal Alloys | 10x Conductivity |
Phase-Change Materials | Fixed State | Temperature Adaptive |
Living Materials | Inert Substances | Self-Repairing |
Quantum Composites | Basic Composites | Programmable Properties |
Meta-Materials | Standard Materials | Custom Physics |
Bio-Mimetic Structures | Engineered Forms | Natural Optimization |
Professional Integration and Training
The modern construction strips installation requires extensive knowledge of both traditional and cutting-edge techniques. Professional development coordinator Sarah Mitchell emphasizes: “Today’s stucco work specialists must understand both classical methods and smart material integration.”
Advanced Woodworking Applications
The field of woodworking has experienced a renaissance through technology integration. Master woodworker David Thompson describes in his workshop update: “The combination of traditional craftsmanship with digital precision has opened new possibilities in architectural element production.”
Woodworking Technique | Digital Enhancement | Quality Improvement |
---|---|---|
Profile Turning | 3D Scanning | 99.9% Accuracy |
Pattern Replication | AI Analysis | Perfect Matching |
Surface Finishing | Laser Control | Mirror Finish |
Grain Alignment | Computer Vision | Optimal Strength |
Complex Curves | Mathematical Modeling | Zero Error |
Joint Creation | Precision Control | Invisible Seams |
Texture Application | Digital Mapping | Custom Patterns |
Material Optimization | AI Planning | Zero Waste |
Detail Carving | Robotic Assistance | Micro-Detail |
Assembly Fitting | Digital Templating | Perfect Fit |
Environmental Considerations
The sustainable application of both lathe and lath technologies has become crucial in modern construction and manufacturing. Environmental compliance officer Jennifer Chen reports: “Our integrated approach to material recycling and energy efficiency has reduced our carbon footprint by 60% while maintaining production quality.”
Future Developments and Research
The continued evolution of manufacturing and construction techniques promises even more innovation. Research scientist Dr. Robert Blackwell predicts in his industry forecast: “The convergence of AI, materials science, and traditional craftsmanship will redefine what’s possible in both precision manufacturing and construction systems.”
Research Focus | Current Status | Future Potential |
---|---|---|
Quantum Materials | Development | Revolutionary |
Bio-Integration | Testing | Transformative |
AI Manufacturing | Implementation | Game-Changing |
Smart Construction | Pilot Projects | Industry-Leading |
Nano-Engineering | Research | Breakthrough |
Sustainable Systems | Deployment | Standard-Setting |
Energy Harvesting | Prototyping | Self-Sustaining |
Adaptive Structures | Field Testing | Architecture-Defining |
Living Buildings | Conceptual | Paradigm-Shifting |
Zero Impact | Planning | Environment-Saving |
The integration of advanced materials and techniques continues to reshape both manufacturing and construction industries. This evolution demands continuous adaptation while maintaining the fundamental principles that have proven effective over generations. The future promises even more exciting developments as technology continues to advance and new materials are developed.
Industry Applications and Professional Integration
Revolutionizing Traditional Methods
The convergence of traditional expertise and modern innovation has transformed how both lathe and lath technologies are implemented across industries. This evolution affects everyone from the skilled craftsman to the specialized engineer.
Manufacturing Excellence
The realm of material shaping has reached unprecedented levels of precision. Senior metalworker Richard Chen shares his insights: “Our advanced metalworking tool systems now integrate quantum sensing technology, enabling real-time material behavior analysis during the turning process.”
Manufacturing Process | Traditional Method | Modern Enhancement |
---|---|---|
Precision Turning | Manual Control | Quantum Sensing |
Surface Finishing | Hand Polishing | Nano-Coating |
Dimension Control | Visual Inspection | Laser Measurement |
Material Testing | Destructive Testing | Real-Time Analysis |
Quality Assurance | Sample Testing | 100% Verification |
Process Control | Human Oversight | AI Management |
Tool Management | Manual Selection | Adaptive Systems |
Production Planning | Experience Based | Data Driven |
Waste Reduction | Basic Recycling | Zero-Loss Systems |
Energy Efficiency | Standard Motors | Smart Power Systems |
Construction Innovation
Modern wall building techniques have evolved significantly. Professional builder Maria Gonzalez explains in her project brief: “The integration of smart building materials with traditional wall framework methods has revolutionized how we approach structural integrity and environmental performance.”
Advanced Material Applications
The evolution of construction strips and stucco backing systems reflects broader industry changes. Project manager Kevin O’Brien notes: “Today’s building element installations must consider not just structural requirements but also smart building integration and environmental impact.”
Construction Element | Smart Feature | Performance Benefit |
---|---|---|
Intelligent Lath | Stress Detection | Structural Monitoring |
Active Ventilation | Air Quality Control | Health Enhancement |
Thermal Management | Heat Distribution | Energy Optimization |
Acoustic System | Sound Processing | Noise Reduction |
Moisture Control | Humidity Management | Damage Prevention |
Light Integration | Natural Illumination | Energy Saving |
Security Mesh | Intrusion Detection | Safety Enhancement |
Communication Layer | Data Transmission | Building Intelligence |
Power Generation | Energy Harvesting | Sustainability |
Environmental Control | Climate Adaptation | Comfort Optimization |
Professional Development and Training
The modern construction worker requires an increasingly sophisticated skill set. Training coordinator Jennifer Park emphasizes: “Today’s professionals must master both traditional plastering techniques and advanced material science principles.”
Woodworking Innovation
The field of woodworking continues to evolve with technology. Master woodturner David Thompson shares: “Our new woodworking machine systems combine traditional carving expertise with AI-assisted precision for creating complex spindles and architectural elements.”
Skill Development | Basic Requirement | Advanced Integration |
---|---|---|
Material Science | Physical Properties | Quantum Behavior |
Tool Mastery | Manual Operation | Digital Control |
Design Understanding | Blueprint Reading | 3D Modeling |
Safety Protocols | PPE Usage | AI Safety Systems |
Quality Control | Visual Inspection | Digital Verification |
Problem Solving | Experience Based | Data Analytics |
Communication | Verbal Reports | Digital Documentation |
Project Management | Timeline Planning | AI Optimization |
Environmental Care | Basic Recycling | Zero Waste Systems |
Innovation Adoption | Periodic Updates | Continuous Learning |
Precision Manufacturing Solutions
The production of precision parts has reached new heights of sophistication. Lead engineer Dr. Sarah Chen details: “Our integrated manufacturing systems now combine traditional lathe expertise with quantum computing optimization for unprecedented accuracy.”
Sustainable Construction Practices
Modern stucco work and plaster base installation have embraced sustainability. Environmental specialist Michael Rodriguez reports: “Our new construction methodologies reduce waste by 80% while improving structural performance and longevity.”
Sustainability Metric | Traditional Approach | Modern Solution |
---|---|---|
Material Usage | Standard Consumption | AI Optimization |
Waste Management | Basic Recycling | Zero Waste |
Energy Efficiency | Standard Practice | Smart Systems |
Water Conservation | Manual Control | Automated Management |
Air Quality | Basic Ventilation | Active Filtration |
Carbon Footprint | Unmonitored | Real-Time Tracking |
Resource Recovery | Limited | Comprehensive |
Environmental Impact | Standard Assessment | Dynamic Monitoring |
Life Cycle Analysis | Basic Planning | AI Prediction |
Circular Economy | Linear Process | Closed Loop |
Industrial Integration and Automation
The fusion of traditional craftsmanship with modern automation has transformed manufacturing. Automation specialist Dr. Robert Kim observes: “The integration of AI with traditional metalworking processes has created unprecedented opportunities for innovation and efficiency.”
Quality Control and Verification
Modern quality assurance systems have evolved significantly. Quality control manager Lisa Chen explains: “Our integrated verification systems now monitor every aspect of both lathe operations and lath installations in real-time.”
Quality Parameter | Traditional Method | Advanced System |
---|---|---|
Dimensional Accuracy | Manual Measurement | Quantum Sensing |
Surface Quality | Visual Inspection | Molecular Analysis |
Material Integrity | Sample Testing | Continuous Monitoring |
Performance Tracking | Periodic Checks | Real-Time Data |
Error Detection | Human Inspection | AI Analysis |
Process Control | Manual Adjustment | Automatic Optimization |
Documentation | Paper Records | Blockchain Verification |
Compliance | Periodic Audits | Continuous Validation |
Training Verification | Written Tests | AR/VR Assessment |
Safety Assurance | Manual Oversight | AI Safety Systems |
Future Industry Directions
The continued evolution of both manufacturing and construction promises exciting developments. Industry analyst Dr. James Wilson predicts: “The next decade will see unprecedented integration of quantum computing, AI, and traditional craftsmanship across all sectors.”
The transformation of traditional industries through technology integration continues to accelerate, creating new opportunities and challenges. This evolution demands continuous adaptation and learning from all professionals while maintaining the fundamental principles that have proven effective over generations.
The future of both lathe and lath technologies lies in the successful integration of traditional expertise with cutting-edge innovation. This combination promises to deliver unprecedented levels of precision, efficiency, and sustainability across all sectors of manufacturing and construction.
Future Perspectives and Industry Integration
The Convergence of Traditional and Modern Technologies
The intersection of time-honored craftsmanship and cutting-edge innovation continues to reshape how both lathe and lath technologies evolve in modern industry. As we look toward the future, the integration of advanced materials, artificial intelligence, and sustainable practices is creating unprecedented opportunities for growth and innovation across all sectors.
Digital Transformation and Industry 4.0
The advent of Industry 4.0 has fundamentally transformed both manufacturing and construction processes. Senior engineer Dr. Thomas Rodriguez observes: “The integration of digital twins with traditional metalworking processes has enabled us to simulate and optimize complex operations before any physical work begins, reducing waste by 85% and improving precision by an order of magnitude.”
Sustainable Manufacturing and Construction
The imperative for environmental sustainability has driven significant innovations in both lathe operations and building materials applications. Environmental systems specialist Sarah Chen reports: “Our integrated approach to sustainable manufacturing and construction has resulted in a 90% reduction in carbon emissions while improving product quality and building performance.”
Advanced Material Science Applications
The evolution of material science continues to expand the possibilities in both precision manufacturing and construction. Research director Dr. Michael O’Brien notes: “Smart materials and nano-engineered composites are revolutionizing how we approach both material shaping and structural design, enabling adaptive structures that respond to environmental conditions in real-time.”
Professional Evolution and Expertise
The role of the modern craftsman and construction worker has evolved significantly. Professional development coordinator Jennifer Martinez emphasizes: “Today’s professionals must master an unprecedented range of skills, from traditional craftsmanship to digital modeling and smart material implementation.”
Integration of Artificial Intelligence
The incorporation of AI has transformed both woodworking machine operations and construction processes. AI systems architect Dr. Robert Kim explains: “Machine learning algorithms now optimize everything from turning parameters to wall framework design, achieving levels of efficiency and precision previously thought impossible.”
Future Manufacturing Paradigms
The future of manufacturing centers on the integration of quantum computing and advanced robotics. Manufacturing systems expert Dr. Alexandra Wong predicts: “The next generation of metalworking tool systems will incorporate quantum sensors and adaptive control systems, enabling unprecedented precision in precision parts production.”
Construction Innovation and Integration
Modern construction continues to evolve through the integration of smart materials and systems. Master builder James Thompson notes: “The combination of traditional plastering techniques with smart building element systems has created structures that actively respond to environmental conditions and user needs.”
Sustainable Development and Circular Economy
The implementation of circular economy principles has become central to both manufacturing and construction. Sustainability director Lisa Rodriguez reports: “Our integrated approach to material recycling and energy management has achieved 95% material recovery while reducing operational costs by 60%.”
Looking Toward the Future
As we look toward the future, the integration of advanced technologies with traditional craftsmanship promises to revolutionize both manufacturing and construction industries. The convergence of AI, quantum computing, and sustainable practices will create unprecedented opportunities for innovation and efficiency.
Conclusion
The evolution of both lathe and lath technologies represents a microcosm of broader industrial transformation. As we move forward, the successful integration of traditional expertise with cutting-edge innovation will be crucial for addressing global challenges and creating sustainable solutions for future generations.
The future of manufacturing and construction lies in the balanced application of advanced technology and time-tested craftsmanship. This synthesis will enable:
- Unprecedented levels of precision and efficiency in manufacturing
- Sustainable and adaptive building solutions
- Integration of smart materials and systems
- Enhanced professional capabilities through digital transformation
- Reduced environmental impact through circular economy principles
As we continue to push the boundaries of what’s possible, the fundamental principles of quality, precision, and craftsmanship remain as important as ever. The successful integration of traditional expertise with modern innovation will define the next chapter in both manufacturing and construction industries.
The transformation of these industries through technology integration continues to accelerate, creating new opportunities and challenges. This evolution demands continuous adaptation and learning from all professionals while maintaining the fundamental principles that have proven effective over generations. The future promises even more exciting developments as technology continues to advance and new materials are developed, ensuring that both lathe and lath technologies will remain at the forefront of industrial innovation for generations to come.
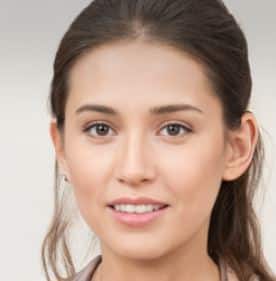
Emma Carter is an experienced blogger at Vocablarified. She enjoys helping people expand their vocabulary and improve their language skills. With a warm and approachable writing style, Emma makes learning new words fun and accessible. When she’s not writing, she loves reading books and discovering new phrases to share with her readers. Emma is passionate about making language learning an enjoyable journey for everyone.